Mechanical Parts Processing-material Forming Manufacturing Process
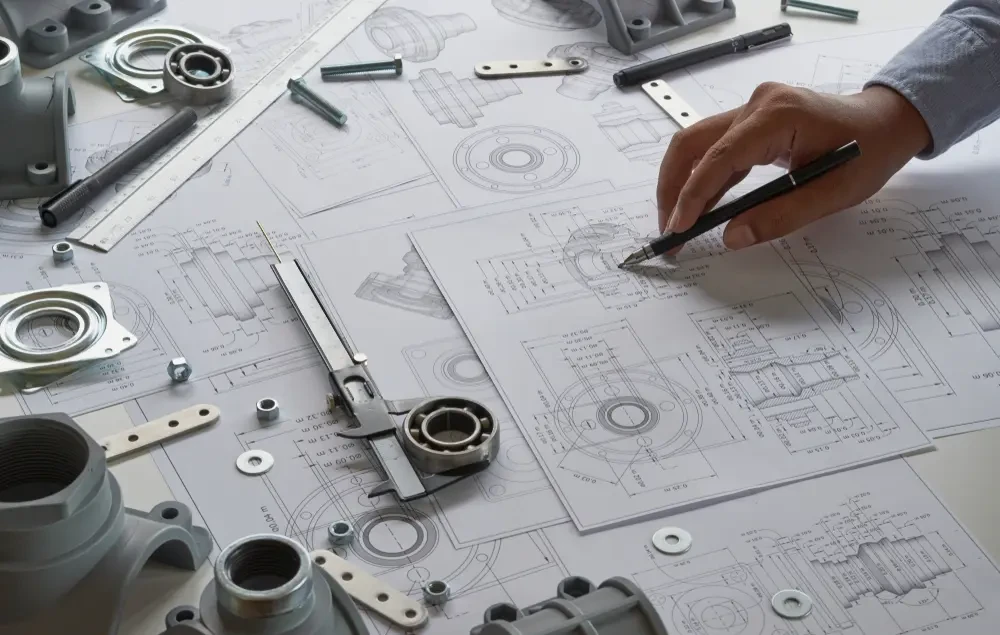
Material forming manufacturing processes mostly use models to make raw materials into parts or blanks. During the material forming process, the shape, size, organizational state, and even the combined state of the raw materials will change.
Since the forming accuracy is generally not high, the material forming manufacturing process is often used to manufacture the blank. It can also be used to manufacture parts with complex shapes but not very demanding precision. The material forming process of machine parts has high production efficiency, and the commonly used forming processes are as follows.
Casting
Casting is a process in which liquid metal is poured into a mold cavity suitable for the shape and size of the part, and the blank or part is obtained after cooling and solidification. The basic technological process is modeling, smelting, pouring, cleaning, and so on.
Because of the filling ability, shrinkage, and other factors during alloy casting, castings may have uneven structure, shrinkage, thermal stress, and deformation, which will make the accuracy, surface quality, and mechanical properties of the castings poor.
Nevertheless, due to strong adaptability and low production cost, casting processing is still widely used. The shape is complex, especially the rough part with a complex inner cavity is often used for casting.
At present, the commonly used casting methods in production include ordinary sand casting, investment casting, metal mold casting, pressure casting, centrifugal casting, and so on. Among them, ordinary sand casting is the most widely used.
Forging
Forging is the use of forging equipment to apply external force to the heated metal for plastic deformation to form a part blank with a certain shape, size, and structure.
The internal structure of the forged blank is dense and uniform. The metal streamline distribution is reasonable, which improves the strength of the parts. Therefore, forging is often used to manufacture blanks for parts that require high comprehensive mechanical properties.
(1) Free forging
Free forging is to place the metal between the upper and lower abutment irons to plastically deform the metal, with a low utilization rate and low precision. Generally used to produce forgings with small batch sizes and simple shapes.
(2) Model forging
Model forging is to place metal in the die cavity of a forging die to deform. The plastic flow of the metal is restricted by the die cavity. The forming efficiency is high, the precision is high, and the metal streamline distribution is more reasonable.
However, due to the high cost of mold manufacturing, it is usually used for mass production. The forging force required for free forging is large and cannot be used for forging large forgings.
(3) Fetal membrane forging
Tire mold forging is to forge metal using tire molds on free forging equipment. Tire molds are simple to manufacture, low cost, and convenient to form, but they have low forming accuracy. They are often used to produce small forgings with low accuracy requirements.
Powder metallurgy
Powder metallurgy is a process in which metal powder or a mixture of metal and non-metal powder is used as a raw material to produce certain metal products or metal materials through mold pressing and sintering processes. It can not only produce special metal materials but also produce metal parts with little and no cutting processing.
The utilization rate of powder metallurgy can reach 95%, which can greatly reduce the investment in cutting and reduce the production cost, so it is increasingly widely used in machinery manufacturing.
Because of the high price of powder raw materials used in powder metallurgy, the fluidity of the powder during forming is poor, and the shape and size of the parts are subject to certain restrictions. There are a certain amount of tiny pores in the powder metallurgy parts, the strength of which is about 20%-30% lower than that of castings or forgings, and the plasticity and toughness are also poor.
The technological process of powder metallurgy production includes powder preparation, compounding, pressing and forming, sintering, shaping, and so on. Among them, the powder preparation and mixing process are usually completed by the manufacturer that provides the powder.
The precision machine parts provided by Zhongken Machinery adopt good material forming and manufacturing technology, and have good mechanical structure and performance. If you want to know more about mechanical parts after reading the above, you can contact us for a comprehensive solution.
As a professional parts manufacturer, we have been advancing with the times since its establishment, committed to providing customers with high-quality and low-cost products, with the purpose of meeting customer needs, and continuing to provide customers with satisfactory products and high-quality services. We have a strict quality inspection system and a comprehensive management system, which can control the details of the products to the greatest extent. If you want to buy our mechanical parts, please don't hesitate to contact us immediately!