5 Calculation Criteria in the Design Process of Machine Parts
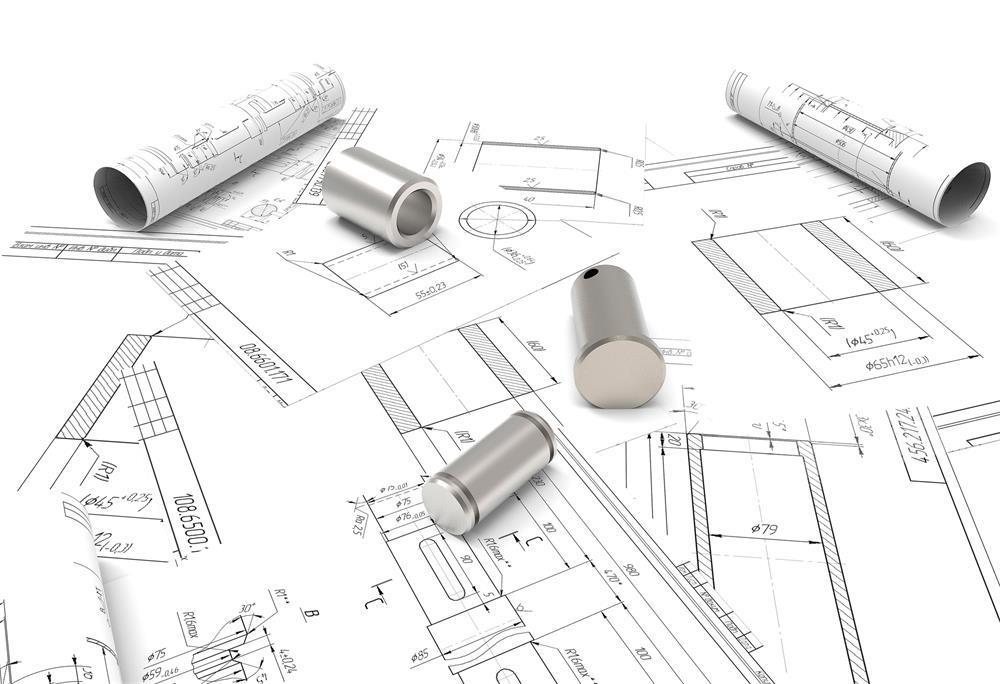
The criteria used to calculate machine parts in the design are undoubtedly closely related to the failure modes of the parts. The accuracy of these calculation criteria is related to the performance of machine parts. Generally speaking, there are roughly the following five calculation criteria.
Strength criterion
The strength criterion means that the stress in the part must not exceed the allowable limit. That is: σ≤σlim
Among them, σlim is the ultimate stress of the material, for brittle materials: σlim=σB (strength limit), for plastic materials: σlim=σS (yield limit).
Taking into account the influence of various contingency or difficult to accurately analyze, the right side of the above formula should be divided by the design safety factor (abbreviated as safety factor), namely: σ≤σlim/S, ie σ≤[σ]
In the formula: the safety factor S is a number greater than 1, if S is too large, it is safe but a waste of materials. S is too small, although it saves materials but tends to be dangerous, so the selection of S should be appropriate. [σ] is called allowable stress.
Stiffness criterion
The elastic deformation y of the part under load is less than or equal to the allowable limit value [y] (allowable deformation) of the machine's performance, which is said to meet the stiffness requirements or meet the stiffness calculation criteria. Its expression is: y≤[y]
The elastic deformation y can be determined according to various deformation theories or experimental methods, and the allowable deformation [y] should be determined according to the theory or experience according to different application occasions.
Life criterion
Since the main factors affecting life—corrosion, wear, and fatigue are three different categories of problems, the laws of their respective development processes are also the same. So far, no effective corrosion life calculation method has been proposed, so it is impossible to list corrosion calculation criteria. Regarding the calculation method of wear, due to its many types, the mechanism of generation has not been fully understood, and the influencing factors are also very complicated, so there is no universal method that can be quantitatively calculated. Regarding the fatigue life, the fatigue limit during the service life is usually calculated as a calculation.
Vibration stability criterion
There are many periodic vibration sources in the machine. For example gear meshing, vibration in rolling bearings, oil film oscillation in sliding bearings, eccentric rotation of elastic shafts, etc. If the natural frequency of a part itself coincides with the frequency of the above-mentioned excitation source or becomes an integral multiple of the relationship, these parts will resonate, resulting in damage to the machine parts or malfunction of the machine working relationship. The so-called vibration stability means that the natural frequency of each part in the machine that is subjected to the excitation is staggered with the frequency of the excitation source. For example, if f represents the natural frequency of the part and fp represents the frequency of the excitation source, the following conditions should usually be guaranteed: 0.85f>fp or 1.15f>fp
If the above conditions cannot be met, you can change the rigidity of the parts and the system, change the support position, increase or decrease the auxiliary support, etc. to change the f value.
Isolating the excitation source from the machine basic parts so that the periodically changing energy of the excitation is not transmitted to the parts; or using damping to reduce the amplitude of the excited vibration parts will improve the vibration stability of the parts.
Reliability criteria
If there is a large number of certain precious machine parts, the number of pieces is N0 to be tested under certain working conditions. If there are still N parts working normally after t time, the reliability R of this part working t time under the working environment conditions can be expressed as R=N/N0
If the test time continues to extend, N will continue to decrease, so the reliability of the part is a function of time.
In the early failure stage, the failure rate drops sharply from a very high value to a certain stable value. The reason for the particularly high failure rate at this stage is the initial defects of the parts and components. If a failure occurs in the normal use stage, it is generally caused by accidental reasons, so its occurrence is random, and the failure rate is expressed as a constant. The damaging stage is mainly due to the long-term use of the parts causing wear and fatigue crack growth, etc., which causes the failure rate to increase sharply.
The design process of machine parts requires a lot of precise calculations, so as to ensure a good working condition in the machine. If you want to know more about machine parts after reading the above content, you can get more relevant knowledge by contacting us.
As a professional parts manufacturer, we have always been committed to providing customers with quality products and services. We have a professional production department and experienced technicians to inspect all aspects of product quality and performance. We can also provide thoughtful one-stop service according to customer needs. If you want to buy our machine parts, please contact us immediately!