How to Remove Burrs from Machine Parts?
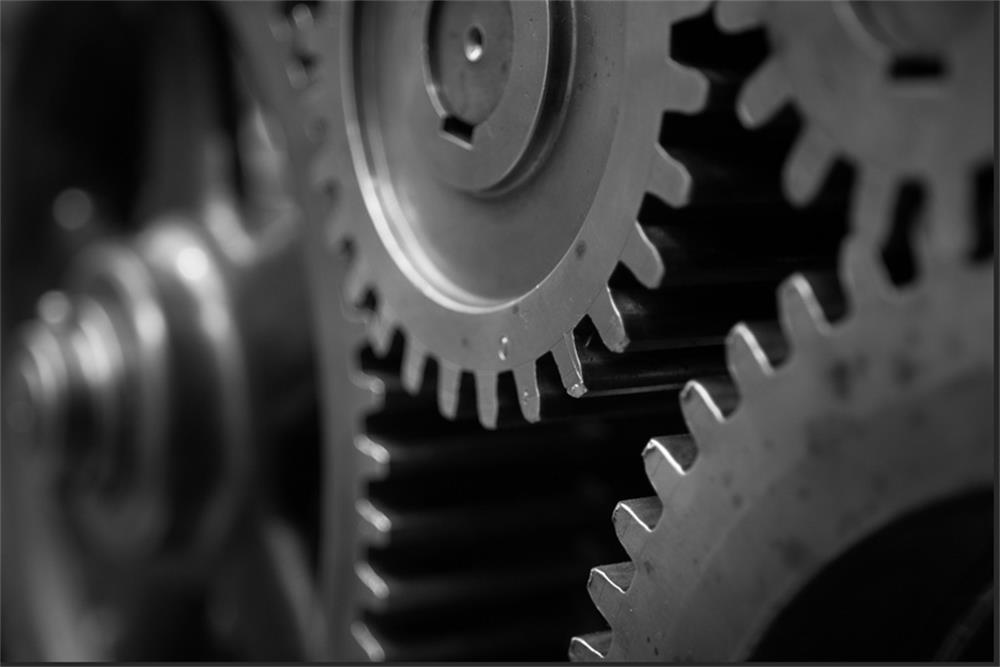
The burr is an inevitable product of metal cutting. It not only affects the appearance of the parts but also affects the quality of the product, which brings trouble and hidden dangers to the subsequent assembly. Therefore, ZHONGKEN has sorted out the following specific methods for removing burrs from machine parts.
1. Electrolytic method
This is to use electrical energy and chemical energy to dissolve the anode to remove burrs. The turbine flowmeter parts are connected to the positive pole of the DC power supply as the anode, the forming tool is connected to the negative pole of the DC power supply as the cathode, and a certain gap is maintained between the two poles to allow the electrolyte to circulate.
Electrolytic deburring machines can be used. When the production batch is not large, the fy4t_3 can be made into a simple device by converting alternating current into direct current with a rectifier.
According to the structure of the part, make a special fixture similar to the shape of the part, which is made of materials with good electrical conductivity such as brass or red copper, and epoxy resin is applied to the unprocessed parts for isolation protection.
2. Chemical method
The cleaned metal parts are placed in a chemical solution, and the metal on the surface of the parts will be transferred to the solution in the form of ions. These ions gather on the surface of the workpiece and form a mucus film with high resistance and low conductivity through a chemical reaction, which protects the surface of the workpiece from corrosion, and the burr protrudes from the surface, and the chemical action will remove the burr. Using the principle of electrochemical reaction, the parts made of metal materials can be automatically and selectively deburred.
3. High-temperature method
The parts that need to be deburred are placed in a tightly sealed chamber, and then a hydrogen-oxygen mixture of a certain pressure is fed. After the spark plug is ignited, the mixture explodes instantaneously, releasing a lot of heat, and the instantaneous temperature is as high as 3300 ℃ or more. Due to the extremely short explosion time, the burrs of the parts are burned away, and other parts of the parts have no time to change.
4. Roll grinding method
Put a certain proportion of the workpiece and abrasive into the closed drum, during the rotation of the drum, the dynamic torque sensor parts and abrasives, parts, and parts are ground to remove burrs. There are special deburring machines and centrifugal rolling polishing machines for rolling and deburring equipment. The abrasives can be quartz sand, sawdust, alumina, ceramics, dolomite, silicon carbide, metal rings, etc.
5. Manual removal method
The traditional method is to manually use steel files, sandpaper, and grinding heads to grind; and the trimming knife gradually replaces these traditional methods, which are simple and convenient to use, do not require technical processing, save costs, and is environmentally friendly.
6. Ultrasonic method
When the ultrasonic energy generated by the ultrasonic wave acts on the liquid in a sparse state of vibration, it will be torn into small cavities (that is, the interior is a vacuum). , and this phenomenon is called cavitation. Ultrasonic deburring is to use the instantaneous impact force of hundreds of atmospheres generated by the "cavitation phenomenon" to remove the burrs attached to the components.
Ultrasonic deburring is not suitable for all burrs, mainly for some microscopic burrs. Generally, if the burrs need to be observed with a microscope, you can try to remove them with ultrasonic waves. For the burrs visible to the naked eye, it mainly depends on the strength of the bond. The burrs with weak bond strength can be treated with ultrasonic waves. Generally, the burrs that can only be treated with a tool can not be treated with the ultrasonic method.
8. High-pressure water jet method
This can use its instant impact to remove burrs and flashes generated after processing, and at the same time achieve the purpose of cleaning. After many tests and tests, the suitable pressure is finally found to be 30MPa-50MPa. If the pressure is insufficient, the effect of deburring cannot be achieved.
Usually, the hydraulic pressure of hydraulic parts in use is within 20Mpa, and the burr residue that cannot be removed with a pressure of 50MPa, the probability of falling off under the working pressure of several MPa is very small.
Now there are more and more manufacturers of high-pressure water deburring equipment, which can be simply classified into two categories: workpiece mobile type and nozzle mobile type. The movable workpiece type has low cost and is suitable for deburring and cleaning simple valve bodies.
The disadvantage is that the fit between the nozzle and the valve body is not ideal, and the burr removal effect of the cross holes and inclined holes inside the valve body is not good; the movable nozzle type is controlled by CNC. It can effectively adjust the distance between the nozzle and the burr-generating part of the valve body and effectively correspond to the burrs of the intersecting holes, oblique holes, and blind holes inside the valve body.
9. Thermal energy method
Thermal deburring is recognized by the world machinery manufacturing industry as the most advanced process for deburring small workpieces in large quantities. It uses hydrogen and oxygen to mix in a closed studio for processing workpieces, ignites and burns instantly, and has a violent thermochemical reaction with the burrs on the surface of the workpiece in a very short time to achieve the purpose of removing burrs.
Thermal deburring is a special processing technology, which has the characteristics of high efficiency, strong versatility, good accessibility, uniform and thorough deburring, and smooth workpiece surface, and is not limited by workpiece material, shape, and burr position.
Because of its extremely high processing efficiency and low direct cost for production, it is especially suitable for use in large-scale continuous production environments and is ideal high-efficiency processing equipment for large-scale industrial production.
8. Frozen trimming method
The thickness of the flash (or burr) of rubber, plastic products, zinc-magnesium aluminum alloy, and other products is much thinner than the thickness of the product, so the embrittlement speed of the flash (or burr) is faster than that of the product.
During this period of time when the product is embrittled (or burr) and the product is not embrittled, the refrigerated deburring (edging) machine removes the embrittled flash (or burr) by hitting the product with projectiles.
A frozen deburring (edge trimming) machine is a machine that uses the ultra-low temperature of liquid nitrogen to rapidly embrittle the flash of rubber, plastic products, and zinc-magnesium-aluminum alloys, and in this state, the frozen particles ejected at high speed hit the product.
The burr (or flash) of the product can be removed, so as to achieve a special deburring (trimming) equipment that can not only remove the burr (or flash) of the product with high quality and high efficiency but also keep all the physical properties of the product itself unchanged. It can greatly improve the trimming (deburring) accuracy of products and has a high degree of intensification.
11. Magnetic deburring machine
The magnetic deburring machine uses its unique magnetic field distribution to produce a strong and stable magnetic induction effect, remove the burr batch front, remove the oxide film and sintering traces. Especially for workpieces with complex shapes, porous cracks, internal and external threads, etc., it can show its magical effect.
Moreover, it does not damage the surface of the workpiece, does not affect the accuracy of the workpiece, and instantly makes the workpiece smooth and tidy, with a new look. This method is suitable for grinding and polishing gold, silver, copper, aluminum, zinc, magnesium, iron, stainless steel, and other metals and non-metallic workpieces such as hard plastics.
The machine parts produced and manufactured by ZHONGKEN have a smooth surface and have been completely removed from burrs, which will not affect the future assembly and use. If you have a need for this, we are undoubtedly your best choice.
As a professional parts supplier, we have advanced processing equipment and strict weight inspection, which can provide customers with high-precision processed parts. And we also provide thoughtful one-stop service, committed to providing customers with good solutions. If you want to buy our high-quality machine parts, please contact us immediately!