How to Measure the Machining Accuracy of Machine Parts?
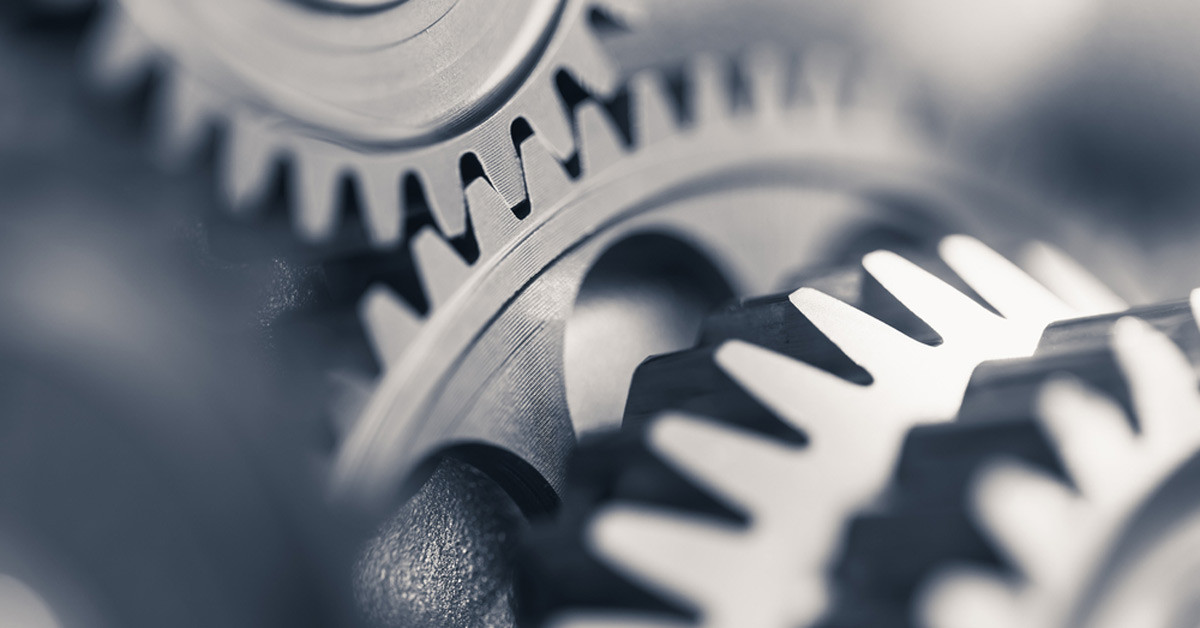
Machining accuracy is the degree of conformity between the actual size, shape, and position of the three geometric parameters of the surface of the processed machine part and the ideal geometric parameters required by the drawing. The processing accuracy adopts different measurement methods according to different processing accuracy content and accuracy requirements. Generally speaking, there are the following types of methods:
Direct measurement and indirect measurement
According to whether the measured parameter is directly measured, it can be divided into direct measurement and indirect measurement.
Direct measurement: directly measure the measured parameter to obtain the measured size. For example, use calipers and comparators to measure. Indirect measurement: Measure the geometric parameters related to the measured size, and obtain the measured size through calculation.
Obviously, direct measurement is more intuitive, and indirect measurement is more cumbersome. Generally, when the measured size or direct measurement fails to meet the accuracy requirements, indirect measurement has to be used.
Absolute measurement and relative measurement
According to whether the reading value of the measuring tool directly represents the value of the measured size, it can be divided into absolute measurement and relative measurement.
Absolute measurement: The reading value directly indicates the size of the measured size, such as measuring with a vernier caliper.
Relative measurement: The reading value only indicates the deviation of the measured size from the standard quantity. If you use a comparator to measure the diameter of the shaft, you need to adjust the zero position of the instrument with a gauge block first, and then perform the measurement. The measured value is the difference between the diameter of the side shaft and the size of the gauge block. This is a relative measurement. Generally speaking, the relative measurement accuracy is higher, but the measurement is more troublesome.
Contact measurement and non-contact measurement
According to whether the measured surface is in contact with the measuring head of the measuring instrument, it is divided into contact measurement and non-contact measurement.
Contact measurement: The measuring head is in contact with the surface being touched, and there is a machine measuring force. Such as measuring machine basic parts with a micrometer.
Non-contact measurement: The measuring head is not in contact with the surface of the measured part. Non-contact measurement can avoid the influence of the measuring force on the measurement result. Such as the use of the projection method, lightwave interferometry, and so on.
Single measurement and comprehensive measurement
According to the number of measurement parameters, it is divided into single measurement and comprehensive measurement.
Single measurement: each parameter of the tested parts of the machine is measured separately.
Comprehensive measurement: measure the comprehensive index reflecting the relevant parameters of machine parts. For example, when measuring the thread with a tool microscope, the actual pitch diameter of the thread, the half-angle error of the tooth profile, and the cumulative error of the thread pitch can be measured separately.
Comprehensive measurement is generally more efficient and more reliable to ensure the interchangeability of precious machine parts and is often used for inspection of finished parts. A single measurement can determine the error of each parameter separately and is generally used for process analysis, process inspection, and measurement of specified parameters.
Active measurement and passive measurement
According to the role of measurement in the processing process, it is divided into active measurement and passive measurement.
Active measurement: the workpiece is measured during the processing, and the result is directly used to control the processing of the part, so as to prevent the generation of waste in time.
Passive measurement: the measurement performed after the workpiece is processed. This kind of measurement can only judge whether the processed part is qualified, and is limited to discovering and rejecting waste products.
Static measurement and dynamic measurement
According to the state of the measured part in the measurement process, it is divided into static measurement and dynamic measurement
Static measurement: The measurement is relatively static. Such as a micrometer to measure the diameter.
Dynamic measurement: The measured surface and the measuring head move relative to each other in the simulated working state during measurement.
The dynamic measurement method can reflect the condition of the machine parts close to the use state, which is the development direction of measurement technology.
The machining accuracy of machine basic parts directly determines the quality of the parts and also affects the quality of the machinery. If you want to know more about machine parts and solutions after reading the above content, you can get it by contacting us.
As a professional parts supplier, we have advanced processing equipment and strict weight inspection, which can provide customers with high-precision processed parts. And we also provide thoughtful one-stop service, committed to providing customers with good solutions. If you want to buy our high-quality machine parts, please contact us immediately!